再生産の検討開始
我々プロジェクトが再生産する部品の検討は、「30年経過した車両の整備で必要な部品」に「外観部品」「過去の注文数が比較的多かった部品」などを観点に加えてひとつひとつ吟味を重ねました。フロントフェンダーは注文数の多さや外観部品であることに加え、ハンドリングやラジエーターへの冷却風影響など機能的にも欠かせない部品であるため当初から再生産部品リストに加えていました。
当時、この部品は本田技研浜松製作所のなかで生産していました。RIM成形という樹脂成形方法で、通常のインジェクション成形(熱で溶かした樹脂を金型内に射出して冷やして固める)とは異なり、低粘度の2種類の樹脂を混合しながら金型に流し込み、その2種類の化学反応によって固まる(2液混合型接着剤と同様)製法です。
現在のモデルで多く用いられる樹脂のインジェクション成形と比較すると、成形時間が多少長くかかるものの金型費が比較的安価であり、当時のRC30生産規模に最適な製造方法でした。しかしながら、生産スピードを重視した他の量産モデルへは波及展開されなかったため、二輪生産を浜松から熊本製作所へ集約するさいに、設備が廃棄されていたことがわかりました。
また、RIM材料についても手元の手描き図と資料では材料グレードが特定できなかったため、フロントフェンダーの再生産は、成形工場と材料探しからスタートしました。
当時の仕様つくりの発掘
当時のつくりを知っている社内のエキスパートを訪ね、材料について聞くと「詳細は材料研究レポートに明記されているはずだ」ということで、関係者にお願いして、30年前の手書きレポートファイルを倉庫の奥から探し出して頂きました。懐かしい手書きのレポートには検討経過からそのテスト結果まで丁寧に記されており、材料グレードもこれで確定できました。
しかし、その材料を供給していただいたお取引先様に連絡をとろうとすると、現在は合併のうえ別会社になっており、そこで改めて新会社に協力をお願いし当時の原材料配合表から、現在も入手可能な同等材料にたどりつくことができました。
RIM成形に関しては、工場内に前述の2種類の材料を共通のタンクに貯蔵し、各成形機へパイプで直接材料供給している場合が多いのでひとつの工場では1つの材料グレードで成形するというのが基本です。いくつかあるRIM材料グレードのうち、RC30用の材料グレードで成形できる工場を探すことになるのですが、それには現在集約されている材料供給メーカー様に紹介していただくのが早道ということになり、結果的に我々の選定した材料を扱っている成形工場はごく少数ということが判りました。
そのなかで、成形〜塗装が一貫してできるお取引先様に連絡を取り、直接生産現場へ伺い、プロジェクトの概要や想いをお伝えしたあと成形工場、塗装工場の現場を拝見させていただき「ここなら、当時の量産品と同じものが生産できる」と双方で確信することができました。
こうしてフロントフェンダーの再生産の道筋をつけることができました。
金型製作のための外観データ
現在は3Dデータをもとに金型加工データをつくっていますが、RC30開発当時は手描き図面で表現しきれない形状は、3Dデータの代わりに2D線図という、立体を等高線のような連続断面で表現した図面をもとに、手で削った木製のマスターモデルを作成し、その形状を倣って金型を削っていました。
RC30のフロントフェンダー木型はRIM成形設備と同様に廃棄されていましたし、お取引先様の現在の金型製作プロセスには立体モデルを倣って金型を削る設備もありません。どうしても3Dデータが必要です。そこで、事情を話してデザイナーに協力を仰ぎ、現物外観面を測定するとともに、設計者が手描き図面の寸法から作成した3Dデータを合体することで、量産当時は存在しなかった製品3Dデータが完成することができました。
できあがった3Dデータを検証するために1/1モデルをつくり実車の部品と比較検証し、更に修正を加えながら30年前の木型形状を現代の3Dデータとして再現できました。
このデータを基にお取引様とRIM成形の方法・金型の法案を何度も協議しました。成形性が難しい箇所もありましたが、RC30のオリジナル形状を再現するという志のもと、お取引様・設計者双方にてアイディアを出し合い、ひとつずつ課題を解決していきました。
こうしたお取引先様やエキスパートの協力のもと、30年前と同じ部品を現代の技術でよみがえらせることができました。
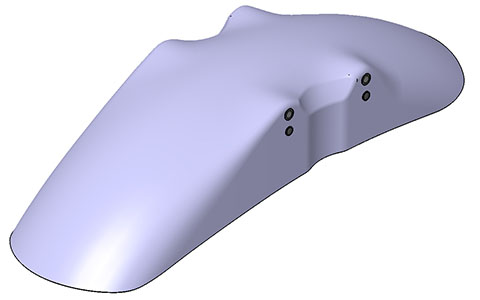
