NSXメカニズム大解剖
9速DCTのヒミツに迫る
6速でも、7速でも、8速でもなく、9速のデュアルクラッチトランスミッション。新型NSXのトランスミッションは、そのスペックだけ見ても「メカ好き」のハートをときめかせてくれる。
「その“中身”を見てみたい」──との想いを抱いて向かったのは、このトランスミッションが製造される、浜松の本田技研工業 トランスミッション製造部 。そこには、心を熱くしてくれるものづくりのドラマも眠っていた。
横置き→縦置きにともなう困難を乗り越えるために
もともとNSXは、車軸とクランクシャフトが同じ方向を向いた「横置き」エンジンで開発が進められていた。そのままデビューに漕ぎ着けていれば、今回の記事でご紹介するほどのトピックが生まれなかったかもしれない。なぜなら、これまでに製造してきたHonda車のトランスミッションの構造を踏襲することができ、おそらくは「粛々と」生産することができたからだ。
ところが、NSXは開発の途上でスーパースポーツとしてトップクラスを狙う動力性能の獲得を目指してターボを搭載。これに伴うメカニズムを高効率に収めるため、エンジンは「縦置き」へと変更された。よって、他のHonda車とは異なり、ピストンの上下運動によって生み出されたクランクシャフト軸の回転方向をハイポイドギアという傘歯車で90度転換させ、ドライブシャフトへと伝える必要が生じる。
大トルクを90度転換させるにはギアに大きな負担がかかる。これに対応するだけでも、より繊細な精度が求められるため生産のためのハードルがひとつ上がることになるが、さらにHondaが採用したのは、縦向きのクランクシャフト軸の回転をハイポイドギアで90度方向転換し、クラッチ前方のクランクシャフト軸のすぐ上を立体交差させて左右にドライブシャフトを貫通させる……という独特のレイアウトだ。
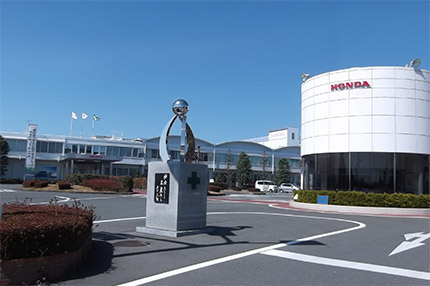
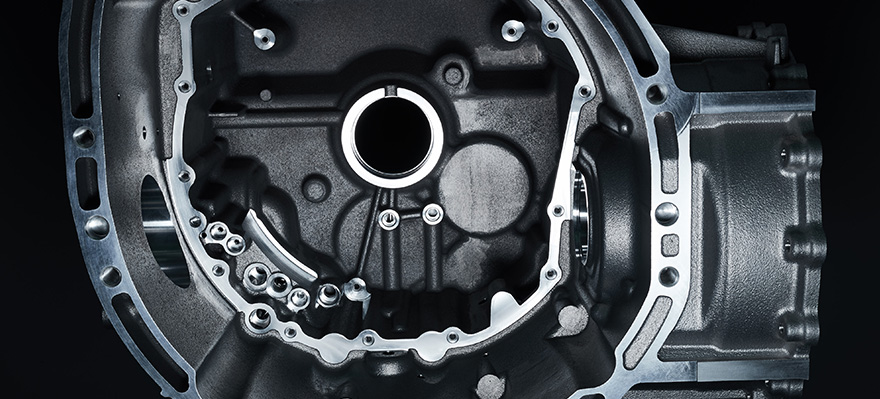
多くのトランスミッションの製造に携わってきた経験豊富なスタッフが「こんな図面、見たことがない……」と言葉を失うほど、常識外れの構造。
トランスミッションのサプライヤーが製造する「既製品」を採用すれば、こんな構造を採用しなくてもクルマはつくれる。だが、それらはあくまでもあらゆる車種に対応できるように作られた「既製品」で、NSXのコンセプトに100%寄り添ってくれるわけではない。特に前後長の長さは開発陣の頭を悩ませた。パワートレインの前後長が伸びることで、ホイールベースもオーバーハングも延長され、スタイリングと運動性能をスポイルさせてしまうのだ。

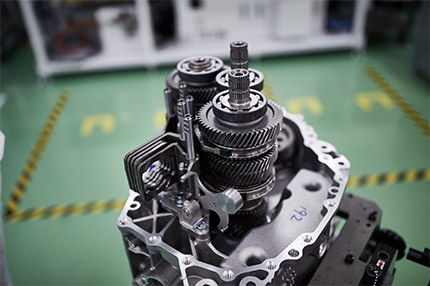
「だからこそ、なんとかしてNSXオリジナルのトランスミッションをつくりたい」──。
開発陣のそんな想いが、Honda創業の地・浜松に根付く「とにかくやってやろうじゃないか、やってみようじゃないか」という「やらまいか精神」に火を付けたという。
トランスミッションは非常に多くのパーツから構成されており、すべてをトランスミッション製造部で手がけることは難しい。量産車種のトランスミッションの生産を行いながら、かつ「初めて」づくしのこのトランスミッションとなれば、なおさらだ。だが、各分野のスペシャリストの力を借りれば、カタチにできるかもしれない。こうして、トランスミッション製造部と協力メーカーの力を結集したチャレンジが始まったのだ。
トランスミッションケースは砂型鋳造
さて、このメカニズムの複雑さは、トランスミッションを収めるケースの造形が物語る。前述した縦置きエンジンであるがゆえの構造に加え、クラッチオイルとギアオイル、それぞれに別々のものを用いるために油路も細かく入り組んでいるのが写真からもおわかりいただけるのではないだろうか。「メカ好き」の心は無条件にときめくが(ときめいた!もっと見たい!壁紙にしてしまいたい!という方はこちらの9速DCTメカニズムギャラリーをどうぞ)、つくるとなると、頭を抱えざるをえないという。
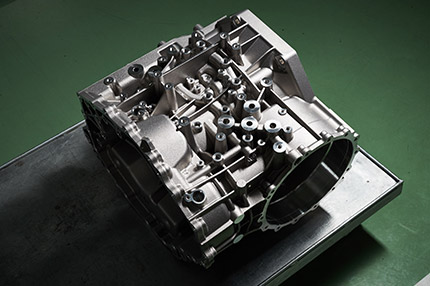
通常のトランスミッションは、金型に溶かした金属を流し込んで作る方法でかたちづくられるのだが、ここまで複雑な構造になると、上下に型抜きするような単純な構造の金型では製造できず、砂型で鋳造しなくてはならない。
溶かした金属を砂でできた型に流し込み、冷えて固まったらまわりの砂を壊して取り除く砂型鋳造は複雑な形状に対応でき、ワンオフのようなパーツには向く一方で製造には手間と時間がかかるために量産に適した手法とは言えない。その上9速ものトランスミッションを収める大きさが必要となると、さらに難しくなる。
トランスミッション製造部、本田技術研究所、ホンダエンジニアリング一丸となって、砂型アルミ鋳造のスペシャリストを探した結果、ついにたどり着いたのが埼玉は羽生にある株式会社田島軽金属(TAC)である。
どのように工程を管理するか?品質を安定させるか?課題は山積していたが、研究所と製造部で各々に専任メンバーを選出し、造りの課題についてはTACのメンバーと協議を繰り返して図面に結び付け、試行錯誤の末に量産に繋がる試作品の製造に成功。その後2基、3基と製造できる台数を増やしていき、最終的に1日に8基を安定供給できる体制を作りあげた。
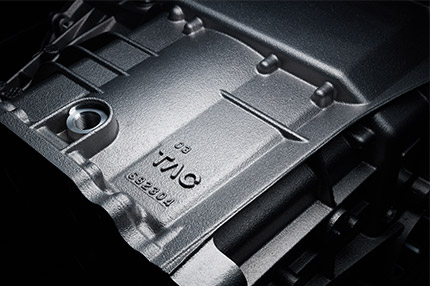
- 1
- 2