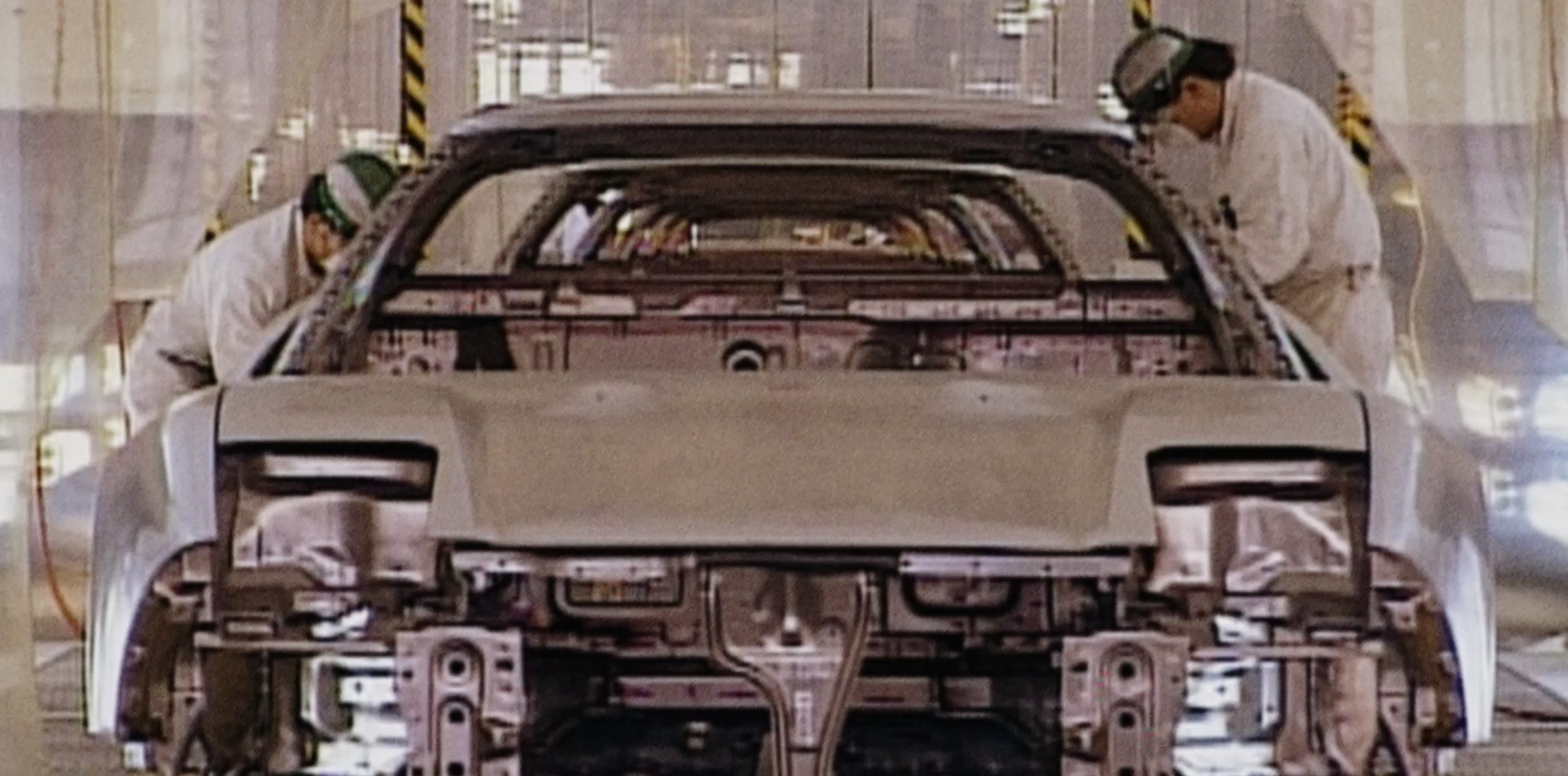
語り継がれる思い Vol.2 NSXヒストリー「軽量化」マイナス200kgへの挑戦2020.11.13
Hondaがめざす新世代スポーツカーNSXのコンセプトは、高性能と快適性が高次元で両立する「快適F1」に決定しました。しかし、実現のためには大きな壁を乗り越えなければなりませんでした。マイナス200kgという非現実的な軽量化です。この無謀とも言える目標に対し、Hondaは軽量金属であるアルミに着目。量産車として世界初となるオールアルミ・モノコックボディーを実現し、エンジン出力に換算して約40PSに匹敵する驚異的な軽量化を達成するとともに、スポーツカーテクノロジーに新たな可能性を拓きました。
■ 目標は5.0kg/PS
「快適F1」へのアプローチはエンジンの検討からスタートしました。Hondaがめざすのは、世界一のビークルダイナミクスを持つミドルウエイトクラスのスポーツカーであり、大きく重い車体を大排気量エンジンで走らせる重量級スポーツカーではありません。そこでまず、重量、重心、パッケージングに優れ、高回転高出力化に有利な直列4気筒2.0リッターエンジンを選択。同時に、パワーウエイトレシオの目標を、当時の大排気量スーパーカーをしのぐ5.0kg/PSに設定しました。5.0リッタークラスのスーパーカーに対し例え最高出力は低くとも、そのぶん軽量であればスーパーカーを上まわる加速性能が得られるうえ圧倒的に優れたハンドリング性能を獲得できます。それはまさに、「快適F1」がめざす「ヒューマンフィッティング」の考え方に一致するものでした。
■ マイナス200kgの壁
パワーウエイトレシオ5.0kg/PSを達成するためには、どのくらい軽く仕上げればよいのでしょう。当時、自然吸気エンジンでは排気量1リッター当たり100PS、2リッターエンジンで200PSが上限でした。つまり車重を1,000kg以下に抑える必要があるのです(5.0kg/1PS=1,000kg/200PS)。当時の2.0リッター量産車は1,130kgほど※1。これにスポーツカーにふさわしい剛性や耐久性を与えるとなると1,200kgを超えることは明らかでした。マイナス200kgという途方もない壁が立ちはだかります。Hondaは、二輪の経験をもとに他の自動車メーカーに先駆けてエンジンのアルミ化を実現し、さらにシャシー部品のアルミ化まで進めていました。その知見とノウハウを最大限に生かしシャシー部品の大半をアルミ化したとしても50kgの軽量化が限界です。残り150kgを削るためには、ボディーの骨格から外板まで、従来とは違った新技術にチャレンジする必要がある、というのがチームメンバーの一致した見解でした。
※1:1985年発売の3代目ACCORD(2.0Si ABS装着車)。
■ 「それならやってみろ」
アルミ部品を適材適所に使い分けるアルミスペースフレームは、いまでこそ他社スーパースポーツなどで採用されていますが、当時はヨーロッパメーカーでさえ実験段階にあり実用化のメドは立っていませんでした。Hondaも先行基礎研究としてアルミの検討はしていたものの、外板への適用が検討されていたにすぎず、骨格を形成するフレームのアルミ化などまったく未知の領域です。それでも「快適F1」を実現するためにはアルミフレームが不可欠だと考えたチームは、アルミフレームと樹脂外板の組み合わせでボディーをつくることを検討しはじめます。しかし、ボディー設計プロジェクトリーダー(PL)※2の考えは異なっていました。「新幹線だって飛行機だってアルミでできている、クルマにできないわけがない」。そして、骨格から外板まですべてをアルミ化したオールアルミボディーを提案したのです。アルミの比重(単位体積あたりの重量)が鉄の3分の1ほどであることは確かです。しかし、クルマの骨格から外板にまで適用するためには、クルマとして必要な剛性・強度耐久性などの課題や、プレス性、溶接性、塗装性など、クリアしなければならない問題が山のように残されており、それらを1つひとつ解決していかなければなりません。研究所の社長※3に報告したところ、「そんなんでおまえ、本当にアルミでできるのか!?」と、叱責にも似た質問が返ってきました。PLも勢いだったのでしょう、「やってみないとわかりません!」と開き直った。「そうか、それならやってみろ!」というのが報告会での結論でした。企業文化というより“人となり”といったほうがいいでしょう。「思い切ってやれ。失敗したって会社がつぶれるわけじゃない。チャレンジして世間をあっと言わせるんだ」。善し悪しは別にして、むかしからHondaにはそういうところがあるのです。
※2:のちの本田技研工業7代目社長・伊東 孝紳。
※3:本田技術研究所(当時)社長、のちの本田技研工業4代目社長・川本 信彦。
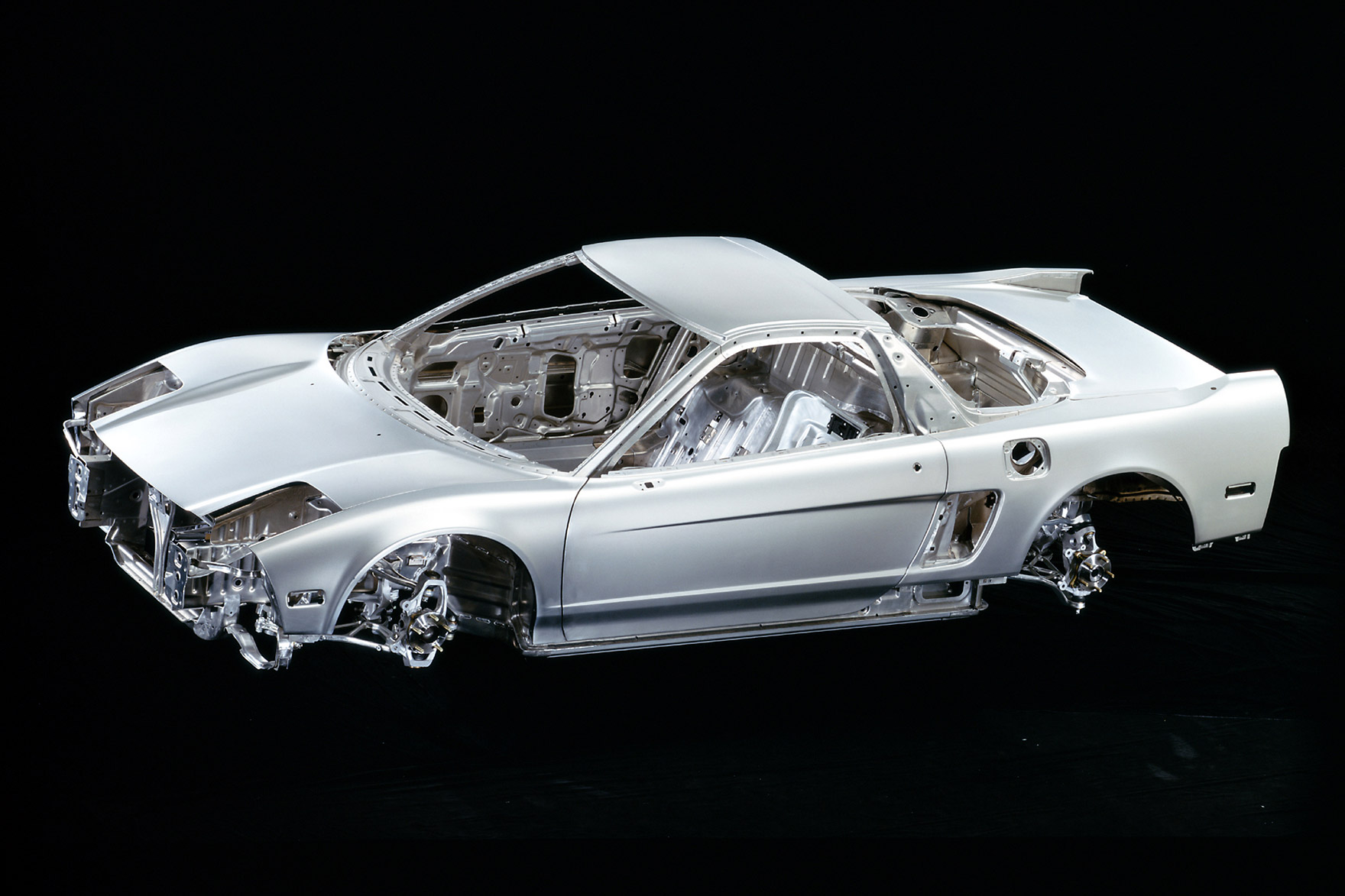
多くの困難を乗り越えて実現した量産車世界初 NSXのオールアルミボディー
■ 「軽さ」という正義
社長の了解も取り付けた。「快適F1」の方向性は、直列4気筒2.0リッターエンジンをミッドシップに搭載した、オールアルミ・モノコックボディーの軽量スポーツカーに定まったかのように思えました。ところが欧米、とりわけアメリカ(American Honda Motor Co., Inc.)の猛反対に遭遇します。当時、北米を中心としたHondaのプレミアムブランド「ACURA」の立ち上げを控えていたアメリカは、イメージリーダーとなるスポーツカーを強く望んでいました。しかし、アメリカの感覚では4気筒はベーシックエンジン。「まったくスポーツカーのフレーバーを感じられない」と言っては6気筒エンジンを搭載するよう一歩も譲りません。アルミボディーに対しても、「パワーウエイトレシオに価値を感じない、コストアップになるから要らない」の一点張りです。世界中を見渡してもどこにもない新世代スポーツカーをつくりたいという思いはまったく受け入れてもらえません。苦渋の選択。巨大市場アメリカが望むV6は飲もう。しかし「快適F1」にとって命とも言える「軽さ」は譲れない。まるでV6と刺し違えるようにして、オールアルミボディーの企画を守り抜いたのです。そうして完成させた量産車世界初のオールアルミ・モノコックボディーは、ホワイトボディー※4比較で鉄製に対しマイナス140kgを達成。エンジンやシャシー部品を含む初代NSXの車重は、従来技術で製作した場合に比べてマイナス200kgという軽量化を実現しました。これは、エンジン出力に換算して実に約40PSの高出力化に相当します。またパワーウエイトレシオも、目標の5.0kg/PSを下まわる4.82kg/PS※5を達成し、初代NSXは、大排気量の重量級スポーツカーをしのぐ加速性能と圧倒的に優れたハンドリング性能を獲得したのです。その軽さは、エンジン負荷の軽減や車体各部への入力の低減をもたらし、部品の長寿命化に貢献。“誰にとっても使いやすく長く愛していただけるスポーツカー”という、当初の願いを叶える原動力ともなりました。
※4:各部品を溶接で組み立てた塗装前のボディー。
※5:初代NSX 5速MT車(1,350kg/280PS)。
■ 「軽さ」の進化と継承
Hondaは、初代NSXで培ったアルミボディー技術の研究をさらに重ね、三次元曲げ成形やダイキャスト成形技術を駆使した低コストなアルミ適用技術を開発。1999年の初代インサイトで、820kg(5速MT車)という軽自動車レベルの車重を実現する新骨格軽量アルミボディーを実現するなど、さまざまなカタチで量産車の軽量化に継承されています。さらに、2代目NSX(2016年)では時代進化した要素技術をフルに活用し、アルミと超高張力鋼管など複合素材技術を新たに開発。外板には、アルミのほかカーボンファイバーやシートモールディングコンパウンド(ガラス繊維強化ポリエステル成形材)を採用するなど、さまざまな素材を適材適所に用いることで、高い剛性と優れた衝突安全性能を達成しながら最大限の軽量化を実現したのです。
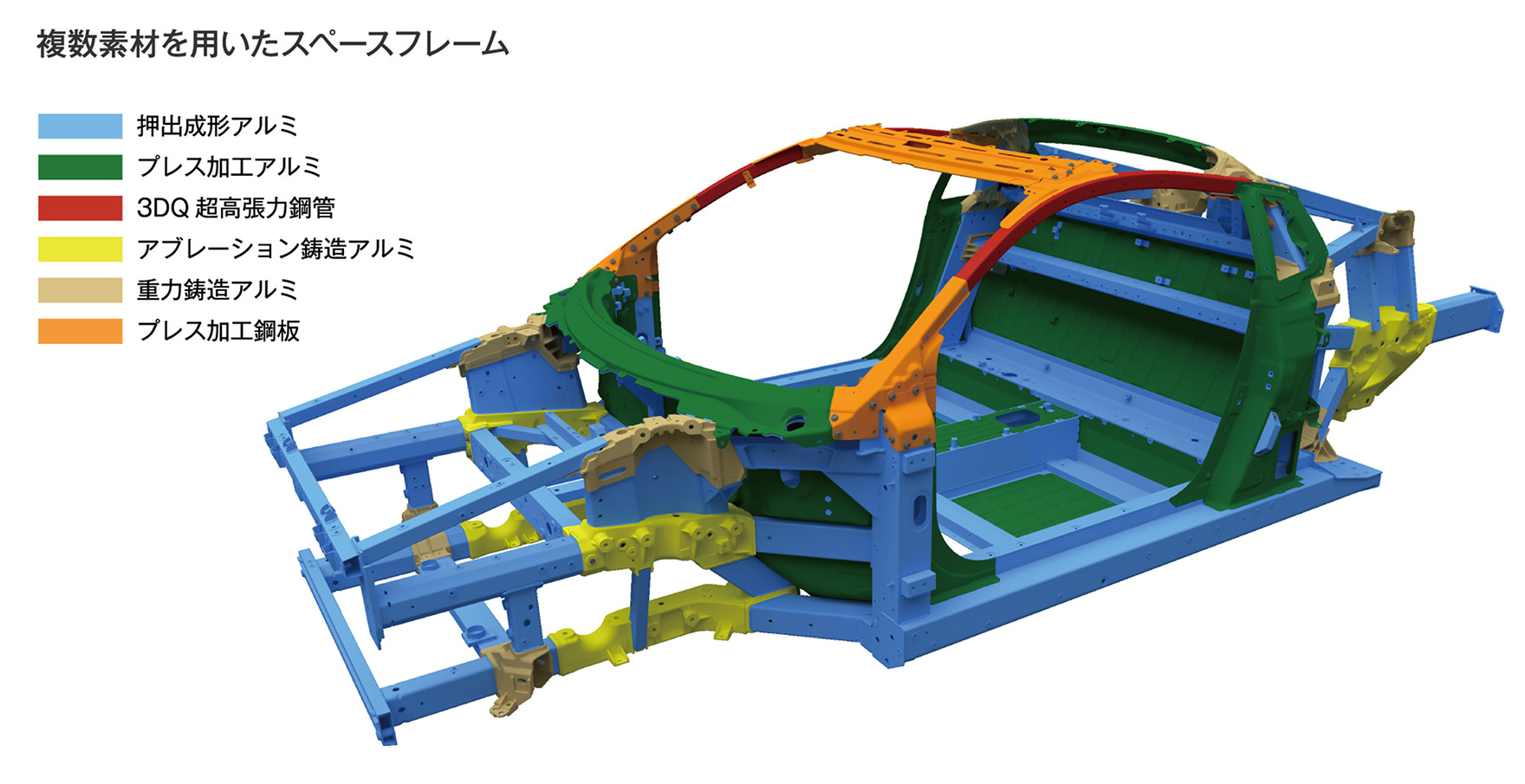